Dry ice blasting | INDUSTRIES APPLICATIONS
Engineered Wood
Contact us Now
Impact of Dry Ice Blasting on:
Engineered Wood
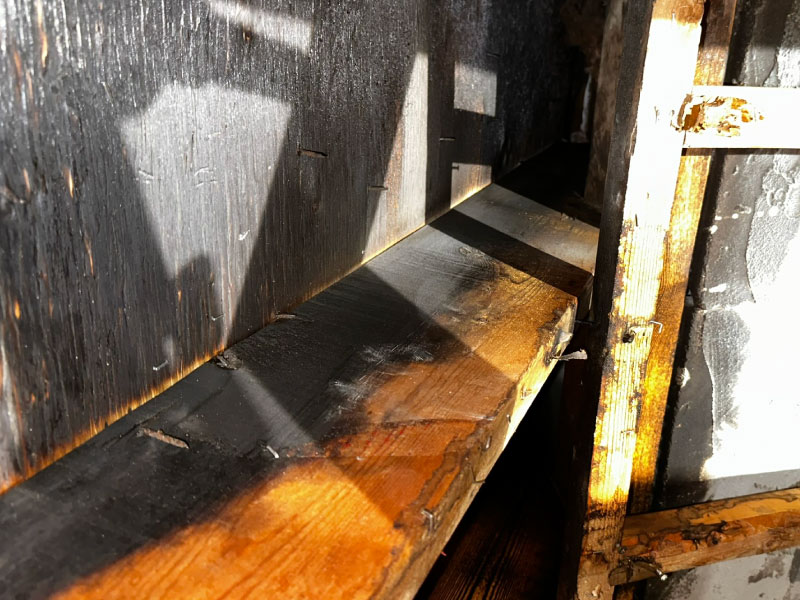
Non-Abrasive Cleaning
Dry Ice Blasting is a non-abrasive method that removes dirt, dust, and contaminants without damaging the delicate surfaces of engineered wood products. It ensures the integrity of the wood and its finishes, which is crucial in the production and maintenance of high-quality engineered wood.
Effective Removal of Residue
In the manufacturing of engineered wood products, residues like adhesives, resin, and sawdust can accumulate on machinery and surfaces. Dry Ice Blasting effectively removes these residues without leaving any secondary waste or damaging the equipment, which helps maintain optimal production efficiency.
No Water or Chemicals
Unlike traditional cleaning methods that may use water or harsh chemicals, Dry Ice Blasting uses solid CO2 pellets, making it ideal for the engineered wood industry. This is important as water can warp or weaken wood products, and chemicals can affect the wood’s finish or structural integrity.
Improves Product Quality
By removing contaminants from production machinery and tools without damaging the equipment, dry ice blasting helps improve the overall quality of engineered wood products. Clean machinery ensures more precise cutting, shaping, and finishing, resulting in higher-quality end products.
Increased Equipment Lifespan
Regular cleaning with dry ice blasting prevents the buildup of debris on machinery, which can cause wear and tear. This leads to less downtime and extends the lifespan of expensive manufacturing equipment used in engineered wood production.
Eco-Friendly and Safe
Dry Ice Blasting is a clean and environmentally friendly method that doesn’t produce harmful chemicals or waste. In an industry that is increasingly concerned with sustainability, this process aligns with eco-conscious goals by minimizing environmental impact.
Efficiency and Reduced Downtime
The speed and efficiency of dry ice blasting mean that cleaning can be done quickly, reducing production downtime. This is particularly important in high-volume operations where minimizing interruptions is crucial to maintaining productivity.
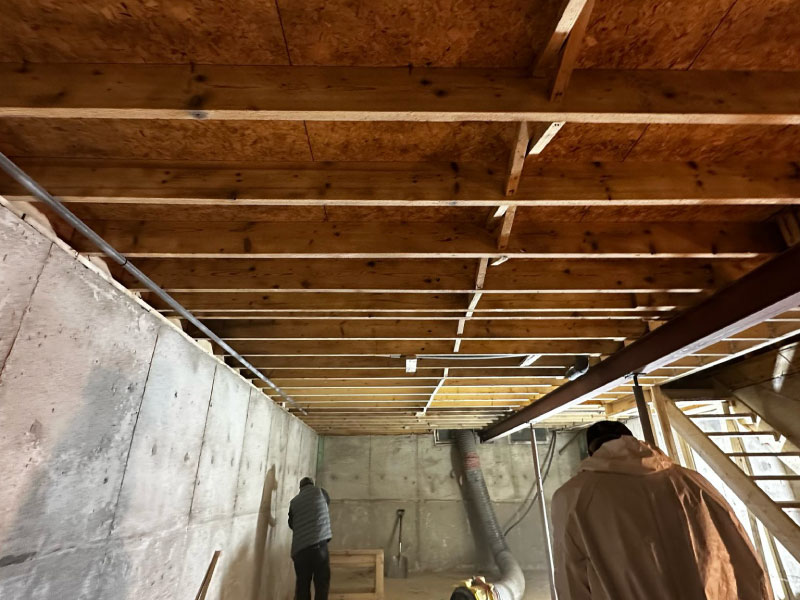